Avoiding Connector Issues on Utility-Scale Solar Sites
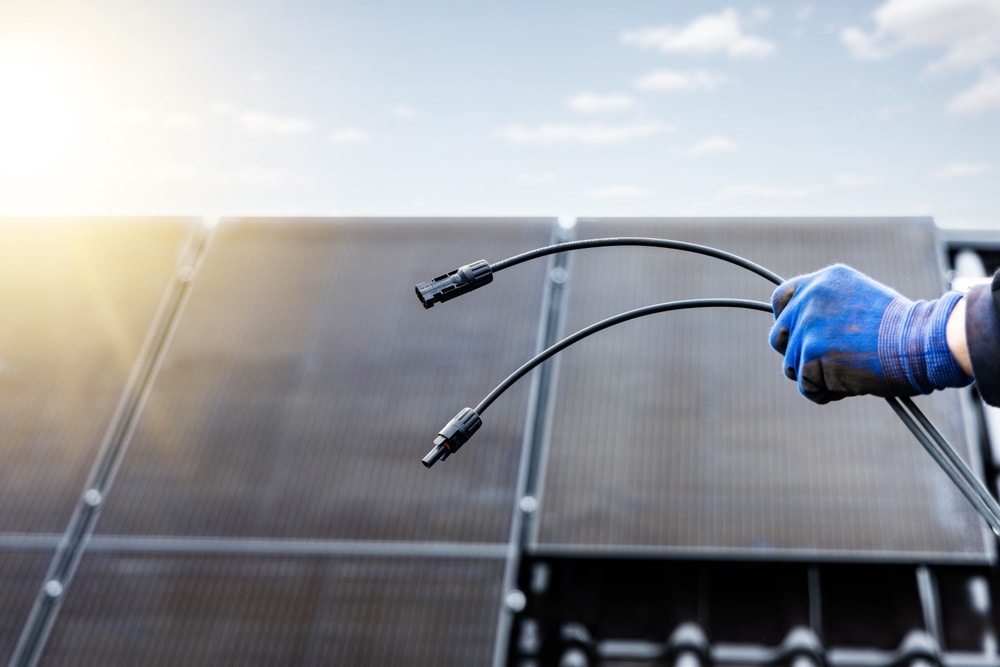
Installation costs, labor, and product reliability often go together when bringing utility-scale solar projects online.
Despite declining hard and soft costs, there is still pressure to deliver projects on time and under budget. This means installers look for every way to save time and money.
Material and labor costs usually provide some savings, but the solutions aren’t always elegant. One issue creeping into the solar conversation is the reliability of PV wire connectors and harnesses that cut down on labor but increase the number of fail points in the balance of system (BOS).
When crews use harnesses, it means more connectors to bring wires together. More connections generally mean more opportunities for issues. Whether it’s installation related, tied to the weather, or just a random event, solar panels can’t do their job if connectors break.
By limiting the number of PV cable connectors, installers reduce the number of fail points and increase reliability.
Why Companies Use Connectors
Every solar project will require MC4 connectors, but the number needed depends on how the installer approaches the problem.
When companies use Sun-Pull bundled PV wire, it’s a 1:1 connection. This means one wire, one string, and one connector from the solar panel to the combiner box. Although the bundle has individual #10 AWG conductors, they can be terminated at different points along the run. As a result, workers only have to move down the line once.
If a company decides to increase the number of connectors used, it would need about half the amount of wire compared to a bundled cable solution. They could also use a larger gauge wire (in this case, #8 AWG) than the #10 AWG used in the bundled wire, reducing electricity lost from the solar panel to the combiner box.
Using connectors across the solar array sounds like a slam dunk, but several drawbacks complicate matters.
No Real Cost Savings
Although the installer needs about half the wire, the larger gauge wire eats into the cost savings. Not to mention, the project now requires harnesses and additional connectors to complete the job. All told, the savings are nearly negligible.
The company might find labor cost savings, which are reduced since workers are installing less wire. Using more connectors saves labor hours, but crews still need to take multiple trips down the line.
“It’s a less elegant method,” Sun-Pull Wire President Nick Eberly explained. “It will cut your labor in half, you only have to go down that row half the number of times because you’re installing a harness, but you’re installing double the number of connectors. You’re also still going down the row multiple times, compared to a bundled wire which requires going down the line once.”
More Connections, More Failure Points
It might not seem like a big deal, but too many connectors can cripple solar installations.
If you’ve ever left something plastic outside, you’ve likely seen firsthand what the elements do to it over time. The same can be said about the plastic housing connectors have that protect the pins and sockets inside.
When joining PV panels to the combiner box, the plastic connector pieces are exposed to the elements, eventually degrading them. Although they’re sunlight resistant, they’re still vulnerable to excess moisture, snow, and other environmental factors. If water sneaks into the connector, it can create a short.
“If you have a piece of wire that’s insulated, that can stay outside for a really long time in the elements,” Eberly explained. “Wherever you put that connector, that’s generally going to fail quicker than the wire itself. And every time one of those connectors blows, a fuse blows too. That lowers the output, and then you have to fix that.”
Eberly suggests a single conductor approach that eliminates as many connectors as possible. In this scenario, a wire runs from the solar panel to the combiner box, keeping sensitive pieces safe while limiting exposure.
It’s Not Always the Connector’s Fault
Sometimes connectors fail through no fault of their own – they get a little help from some unlikely sources.
The products widely used today are called MC4 connectors and were developed by Staubli, a Swiss manufacturer. Although the company owns about one-third of the product’s global market share, hundreds of global connector manufacturers exist, mostly in Asia. Unfortunately, there isn’t a universal standard, meaning manufacturers can produce similar products with subtle differences that could impact performance.
Beyond manufacturing, installers may cause connector failures. From putting connectors on backward and not crimping them hard enough to crimping the surrounding wire insulation, cross-threading, or under/over-torquing them, problems can occur.
As a result, issues could range from a loss of electrical output and performance to full-blown fires.
According to a 2019 Fraunhofer Institute for Solar Energy Systems report, many connector failures found on utility-scale solar arrays happen within the first five years. Additionally, a joint study by PVEL and HelioVolta found connector issues in more than 70% of commercial and industrial projects analyzed by HelioVolta.
With so many variations on the market, it’s difficult to ensure quality, leading to potential delays and setbacks. And when harnesses are used, connector failures often mean the whole harness needs to be replaced.
Small Parts, Huge Impact
Connectors may not seem like a big deal, but there’s a cascading effect whenever one fails.
Let’s say a connector fails at a large solar project. The system loses output because of the damaged connector, and the piece could create a situation where arcs, sparks, or fire occur.
When that happens, the utility or company has to pay labor costs for workers to go out and fix the damage and material costs for a new connector, PV wire, and other BOS parts. The company also loses money because the system isn’t generating as much power, leading to lower profits and potentially unhappy customers.
This isn’t to say every connector failure will cost hundreds of thousands of dollars to repair. But when multiple connectors fail on a large site, several tiny problems can become a giant headache.
One (String) and Done
There isn’t one way to wire a utility-scale solar power site, but it’s possible to save time, labor, and money by finding a system that works well for you.
Bundled PV wire is a simple solution that reduces fail points from the solar panels to the combiner box and lets workers travel each row once. There’s also no need for harnesses or multiple connection points to connect wires. It’s a safer, more reliable system with less risk of failures, such as electrical arcing or dangerous contact with DC electricity.
Like other types of renewable energy, solar is on the rise. Of course, work must be done to fully standardize the process, but the necessary steps are taking place. According to PVEL, the NEC was revised in 2020 to require connector pairs to be tested and certified for intermateability. It’s one small step toward a universal process in the United States.
Connectors are only one piece of a solar BOS, but they’re a potential weak point. Finding solutions that need fewer parts and are more reliable makes it easier to save money on future projects and speeds up the nation’s move away from fossil fuels.